The quality difference can’t be realized until you know more about performance / practice.
(1) Personnel info.
a harmonious, enthusiastic and efficient team of well-trained workers, professional technicians and rigorous analysts.
(2) Facility & system info.:
- Water purification of RO membrane
- Lab Accredited as per ISO / IEC17025
- ISO 9001:2015
- FSSC 22000 / HACCP
- FSMA
- Kosher and Halal
- Non GMO
(3) Material
Material receiving policy is effectively and strictly enforced.
Material suppliers are carefully selected and pre-approved.
(4) Processing water
Unique feature: All processing water for production are purified by RO membrane system. This way, Soy protein of low impurity is achieved.
(5) Production procedure management / Critical control points are fully enforced
- Production is carried out at clean workshop
- well-trained workers are there carefully checking every processing stage;
- QC personnel keep accompany of each working shift for the processing quality control,
- Production line is CIP cleaned routinely
- Workshop cleanness status is checked and tested (via sampling) regularly
(6) Release policy is strictly practised
- The materials and product and sample-kept are clearly marked, labeled, stored and well recorded.
- Lot to Lot is tested by our rigorous QC personnel.
- the tests (especially the microbial ones) are performed on inner control Lot - based on production shift and product packed from which mixing tank (before packing, the product is well mixed there for uniform quality).
- Functional properties (ball-forming; gelling strength; water holding capacity; fat retention capacity; dispersion; viscosity etc) are carefully evaluated
- Meanwhile, samples are regularly sent to third party Lab for testing.
(7) Container-loading
The goods delivered to our partners in good condition, by:
- It is loaded at plant by our own workers & no rough handling.
- The container floor is cleaned before loading,
- The container floor / sides lined with Plastic film to protect bags for floor loading.
(8) Feedback & development
Your valuable comment is always highly appreciated
(9) How your orders are taken good care of
- Make sure the customers’ quality requirement
- clear Order instruction (in Chinese & in form of check-list, covering production, quality control and container loading etc ) released to our plant people involved
- Make sure that the customers’ requirement is fully understood by our plant people
This way:
- Max avoid the problem from root, not by after sales
- Customers’ requirement won’t be ignored or missed, since it is in form of check-list in local language
- We are certain that during the whole chain, there are right people do taking care of your order
- We are confident about the quality actually delivered to our partner.
To work with Unison, “you” are in control
Factory info.:
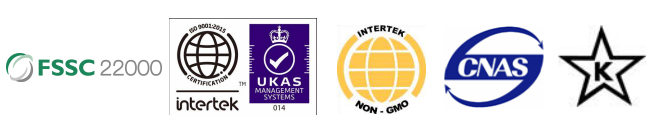